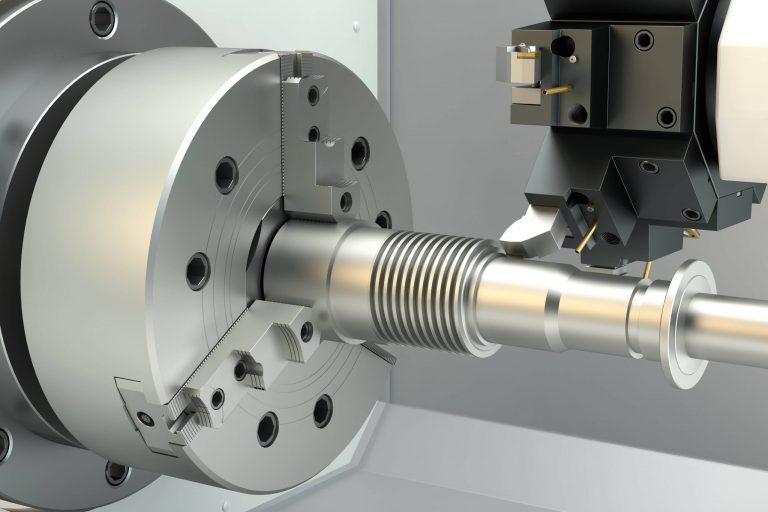
CNC Turning
CNC turning is a machining process used to produce cylindrical parts by removing material from a workpiece as it rotates. Here are the typical steps involved in CNC turning:
1. Prepare the Workpiece
- Select the raw material for the part, usually a round bar or other shape suitable for turning.
- Cut the material to a manageable length if necessary.
- Ensure the material is securely mounted in the CNC lathe’s chuck.
2. Set Up the CNC Lathe
- Install and secure the appropriate cutting tools in the tool turret or holder, based on the required operations (e.g., roughing, finishing, threading).
- Calibrate the tools by setting tool offsets in the machine to ensure precise tool positioning.
- Adjust the machine settings (spindle speed, feed rate, depth of cut) according to the material and desired finish.
3. Create or Load the CNC Program
- Program the machine using G-code, which includes instructions on tool movements, spindle speed, feed rate, and other parameters.
- Load the CNC program if it’s pre-written or created in CAM software based on the design’s CAD model.
- Double-check the code for accuracy to prevent tool collisions or other errors.
4. Run a Dry Run (Optional)
- Perform a “dry run” without material (or at a very low speed) to simulate the toolpath and verify that the tool movements align with the desired part geometry.
- Make adjustments to the program if necessary.
5. Start the Machining Process
- Initiate the turning operation by starting the spindle, which rotates the workpiece.
- The cutting tools move along the programmed paths, gradually removing material to shape the workpiece.
- Common operations include:
- Facing: Flattening the face of the workpiece.
- Turning: Shaping the outer diameter.
- Boring: Enlarging an existing hole.
- Threading: Cutting threads.
- Grooving: Creating recesses.
6. Monitor the Process
- Watch for tool wear, unusual vibrations, or temperature changes during machining.
- Adjust coolant flow if necessary to reduce heat and improve tool life.
- Make minor adjustments as needed to maintain dimensional accuracy.
7. Finish and Inspect the Part
- Complete the turning operations and remove the finished part from the chuck.
- Inspect the part’s dimensions, surface finish, and other features to ensure it meets specifications.
- Perform any additional post-processing, such as deburring or polishing, if needed.
8. Clean Up and Document
- Clean the machine and remove any swarf (metal chips) generated during turning.
- Record relevant data, like cycle time, tooling used, and machine settings, for future reference or repeatability.
Each step requires precision to ensure high-quality, accurate parts are produced. CNC turning can be further optimized by selecting the right tools, speeds, and feeds based on the material and part requirements.
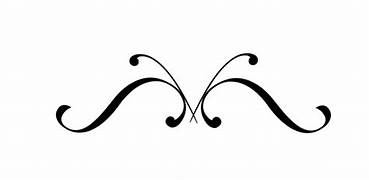