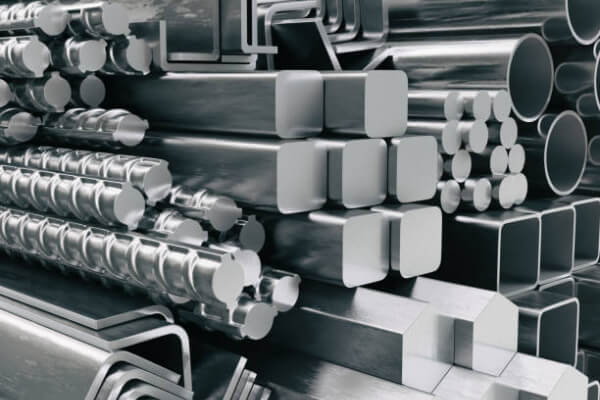
When selecting materials for CNC (Computer Numerical Control) machining, it’s crucial to consider various factors that impact the performance, cost, and end-use of the final product. CNC machining can be applied to a wide range of materials, and each material has its own set of characteristics that influence how it is processed and what applications it is best suited for. Below is a general overview of common CNC materials and the factors to consider when choosing them:
1. Aluminum Alloys
- Description: Aluminum is a lightweight, corrosion-resistant, and easily machinable material that is commonly used in CNC applications. It’s available in various alloys, such as 6061, 7075, and 2024, each offering different strengths and characteristics.
- Key Features:
- High strength-to-weight ratio
- Corrosion resistance (especially 6061)
- Excellent machinability
- Good thermal and electrical conductivity
- Applications: Aerospace, automotive, electronics, consumer goods, and structural components.
- Machining Considerations: Aluminum alloys generally offer a good balance between ease of machining and strength. They can be machined at higher speeds and are often used for both prototypes and production runs.
2. Steel Alloys
- Description: Steel is one of the most versatile and widely used materials in CNC machining. It is available in a variety of alloys, including carbon steels, stainless steels, and tool steels, each offering different mechanical properties.
- Key Features:
- High tensile strength
- Wear resistance (especially tool steels)
- Can be heat-treated for added hardness
- Applications: Structural components, machinery parts, automotive, tooling, and medical devices.
- Machining Considerations: Steel alloys are generally tougher to machine than aluminum, requiring more advanced tools and slower feed rates. Some alloys, like stainless steel, may also require specific machining techniques due to their hardness and tendency to work-harden.
3. Titanium Alloys
- Description: Titanium is known for its high strength, low weight, and excellent corrosion resistance. It is often used in demanding applications such as aerospace and medical industries.
- Key Features:
- Exceptional strength-to-weight ratio
- Excellent corrosion resistance
- High temperature tolerance
- Applications: Aerospace, military, medical implants, high-performance automotive parts.
- Machining Considerations: Titanium is more difficult to machine compared to aluminum and steel due to its toughness and tendency to work-harden. Special tooling and slower speeds are often required to prevent excessive heat buildup.
4. Plastics (e.g., ABS, Nylon, PEEK, Acrylic)
- Description: Plastics are commonly used in CNC machining for creating lightweight, cost-effective, and versatile parts. Materials like ABS, Nylon, PEEK, and acrylic offer different balances of mechanical properties and aesthetic appeal.
- Key Features:
- Lightweight and durable
- Can be transparent (e.g., acrylic)
- Easy to machine, especially softer plastics like ABS and Nylon
- Applications: Prototyping, consumer products, medical devices, automotive, and electronic housings.
- Machining Considerations: Plastics are generally easier to machine than metals, but care should be taken to avoid melting or warping due to heat buildup. Some materials, such as PEEK and PTFE, are more difficult to machine and may require special tooling.
5. Copper and Copper Alloys
- Description: Copper and its alloys, such as brass and bronze, are known for their excellent electrical conductivity, thermal properties, and corrosion resistance.
- Key Features:
- High electrical and thermal conductivity
- Corrosion resistance
- Good machinability
- Applications: Electrical connectors, heat exchangers, plumbing fittings, and decorative items.
- Machining Considerations: Copper is relatively easy to machine, though care must be taken with high-speed operations to avoid overheating and work-hardened surfaces. Some alloys like bronze can be more challenging to machine.
6. Composites (e.g., Carbon Fiber, Fiberglass)
- Description: Composites, such as carbon fiber or fiberglass-reinforced plastics, are strong, lightweight materials often used in industries where weight is a critical factor.
- Key Features:
- High strength-to-weight ratio
- Can be tailored for specific properties (e.g., stiffness, flexibility)
- Excellent corrosion and fatigue resistance
- Applications: Aerospace, automotive, sporting goods, and industrial applications.
- Machining Considerations: Composites require special attention to tool selection, as they can be abrasive and may cause excessive wear on cutting tools. Additionally, carbon fiber composites can produce fine dust that needs to be managed for health and safety.
7. Brass and Bronze
- Description: Brass is an alloy of copper and zinc, while bronze is typically made of copper and tin. These materials are known for their machinability, aesthetic properties, and resistance to corrosion.
- Key Features:
- Excellent machinability (brass)
- Corrosion and wear resistance (bronze)
- Good for creating intricate, small parts
- Applications: Electrical connectors, gears, plumbing, and decorative hardware.
- Machining Considerations: Brass is relatively easy to machine due to its softness, but bronze may require more careful handling due to its toughness. Both materials are prone to work-hardening, especially during high-speed machining.
8. High-Performance Alloys (e.g., Inconel, Hastelloy)
- Description: High-performance alloys like Inconel and Hastelloy are designed to withstand extreme conditions, including high temperatures, corrosion, and oxidation.
- Key Features:
- Excellent high-temperature and corrosion resistance
- High strength in extreme environments
- Applications: Aerospace, nuclear, chemical processing, and high-temperature industrial applications.
- Machining Considerations: These materials are typically very difficult to machine, requiring specialized tooling, cooling systems, and slower feed rates to prevent tool wear and part distortion.
Factors to Consider When Choosing CNC Materials:
- Strength and Durability: Choose materials with appropriate mechanical properties based on the expected load and stress on the part.
- Corrosion Resistance: If the part will be exposed to harsh environmental conditions, corrosion resistance (e.g., aluminum, stainless steel, or titanium) should be prioritized.
- Machinability: Some materials are easier to machine than others, which can impact the cost and time required for production.
- Cost: High-performance materials like titanium and composites are typically more expensive than metals like aluminum or plastics.
- Aesthetic Requirements: Certain materials (e.g., acrylic, brass, or anodized aluminum) are chosen for their visual appeal or finish quality, especially for consumer-facing products.
- Temperature Resistance: For applications in high-temperature environments, materials like Inconel or stainless steel may be necessary.
By carefully considering these factors, you can select the ideal material for your CNC machining project that balances performance, cost, and production efficiency.
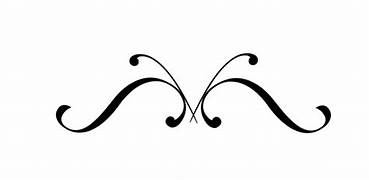