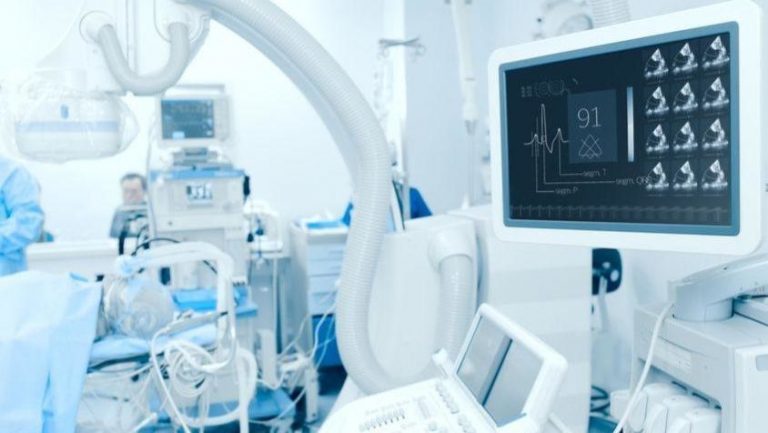
The process of using Computer Numerical Control (CNC) machines to manufacture medical devices typically involves several well-defined steps to ensure precision, quality, and compliance with regulatory standards. Here’s an outline of the typical steps your company can follow:
1. Concept Design and Requirements Gathering
- Define device specifications: Collaborate with biomedical engineers and clinicians to determine the device’s dimensions, materials, and functionalities.
- Create a CAD model: Use software like SolidWorks, AutoCAD, or Fusion 360 to design a detailed 3D model of the device.
2. Material Selection
- Choose biocompatible materials such as stainless steel, titanium, PEEK, or medical-grade polymers, depending on the device’s application.
- Ensure materials meet ISO 10993 (biological evaluation) standards for medical devices.
3. CNC Programming
- Convert the CAD model into CNC machine-readable instructions using CAM software (e.g., Mastercam, Fusion 360, or GibbsCAM).
- Define tool paths, cutting strategies, and speeds to achieve precise tolerances.
4. Prototype Development
- Manufacture a prototype for initial evaluation.
- Test for functionality, structural integrity, and compliance with medical standards.
- Iterate designs based on feedback from testing and stakeholder reviews.
5. Validation and Regulatory Compliance
- Perform design validation: Ensure the device meets functional and safety requirements.
- Document manufacturing processes for compliance with ISO 13485 (Medical Devices Quality Management System) and FDA regulations.
- Conduct risk assessments under ISO 14971 (Risk Management for Medical Devices).
6. CNC Machining
- Set up the CNC machine and load the material.
- Run the CNC program to manufacture the device components.
- Use quality control tools (e.g., probes, calipers) to monitor dimensions and tolerances during machining.
7. Surface Finishing and Post-Processing
- Perform deburring, polishing, or coating to meet medical device standards for cleanliness and smoothness.
- Apply any necessary surface treatments (e.g., passivation for stainless steel or anodizing for titanium).
8. Quality Assurance and Testing
- Inspect components for precision using Coordinate Measuring Machines (CMMs), optical scanners, or microscopes.
- Conduct functional tests, such as mechanical stress testing or biocompatibility assessments.
9. Assembly and Packaging
- Assemble individual components if required.
- Package devices in sterile conditions according to ISO 11607 (Packaging for Terminally Sterilized Medical Devices).
10. Sterilization and Delivery
- Sterilize the devices using approved methods (e.g., gamma radiation, ethylene oxide, or autoclaving).
- Label and document for traceability per UDI (Unique Device Identifier) regulations.
- Ship to customers or distributors.
11. Continuous Improvement
- Gather feedback from end-users and regulatory audits.
- Update manufacturing processes and designs as needed to improve efficiency and compliance.