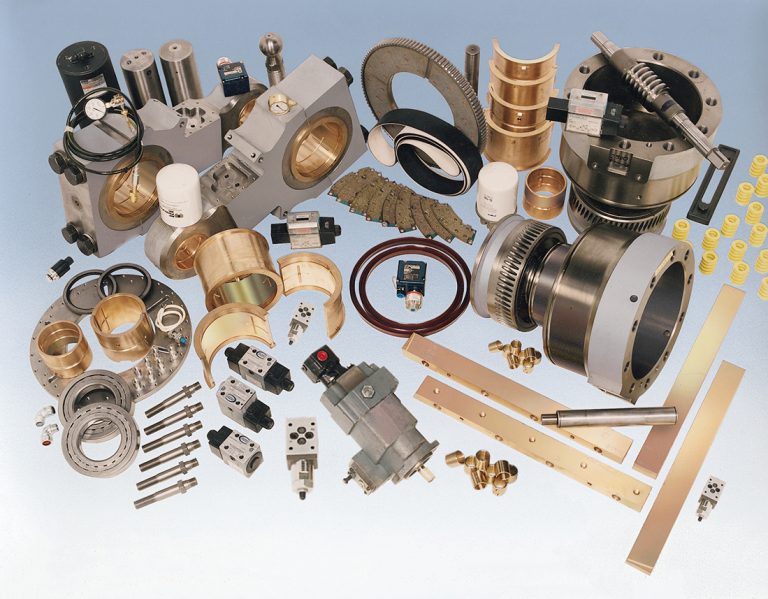
Automation
In CNC machining, automation plays a crucial role in improving efficiency, precision, and repeatability. Here are some essential automation components commonly used in CNC systems:
1. Automatic Tool Changer (ATC)
- The ATC allows CNC machines to switch between different cutting tools without manual intervention. The tool changer selects, grabs, and places the required tool into the spindle based on the program sequence.
- Benefits: Reduces downtime, enables complex machining operations, and allows for unattended machining with multi-tool requirements.
2. Pallet Changer and Workholding Automation
- A pallet changer is used to load and unload workpieces automatically. It swaps the finished workpiece with a new one while the machine continues running.
- Automatic Workholding Systems: These include hydraulic or pneumatic clamps that secure the workpiece without manual clamping.
- Benefits: Minimizes setup time, improves workflow efficiency, and allows for continuous, high-volume production.
3. Robotic Arm Integration
- Robotic arms are increasingly used for loading and unloading workpieces, changing pallets, and even moving parts between different machines for various operations.
- Benefits: Allows fully automated, multi-process machining with minimal human intervention, and significantly increases throughput in a production line.
4. Chip Conveyor and Coolant Management Systems
- Chip conveyors automatically remove swarf (metal chips) from the machine area, while coolant management systems maintain optimal coolant levels, filter out debris, and recycle coolant fluid.
- Benefits: Improves machine cleanliness, enhances cutting quality, and reduces manual cleanup and maintenance.
5. Probing and Inspection Systems
- Tool Probing: Automated tool probes check the length, diameter, and wear of tools to ensure accuracy and adjust offsets in real time.
- Workpiece Probing: Automated touch probes can locate and inspect parts, ensuring alignment, positioning, and feature accuracy before and after machining.
- Benefits: Reduces errors, improves dimensional accuracy, and enables in-process quality control for consistent part quality.
6. Computer Numerical Control (CNC) Controller Automation
- Modern CNC controllers automate machine parameters, manage toolpaths, monitor tool wear, and adjust speeds and feeds automatically based on programmed logic and real-time conditions.
- Benefits: Enhances control over machining parameters, maximizes tool life, and adapts to changing material conditions dynamically.
7. Automatic Lubrication Systems
- Automated lubrication systems apply lubricants to the machine’s moving parts, reducing friction, wear, and heat buildup.
- Benefits: Reduces maintenance downtime, increases machine longevity, and ensures optimal machine performance.
8. Automatic Material Handling and Feeding Systems
- These systems involve conveyors, feeders, or automated carousels to load raw materials or cut blanks directly into the CNC machine.
- Benefits: Allows for uninterrupted production runs, enhances workflow efficiency, and reduces manual material handling time.
9. Automated Data Collection and Monitoring Systems
- These systems use sensors and IoT technology to monitor machine status, tool wear, production rates, and maintenance needs in real-time.
- Benefits: Enables predictive maintenance, minimizes downtime, and provides valuable insights for process optimization.
10. Lights-Out Manufacturing
- With advancements in automation, CNC machining systems are now capable of operating without human intervention (often overnight), referred to as “lights-out” manufacturing.
- Benefits: Maximizes machine utilization, reduces labor costs, and enables high-output production over extended periods.
11. Bar Feeders (for CNC Lathes)
- Bar feeders automatically feed bars of material into CNC lathes, allowing the machine to produce multiple parts in a continuous sequence.
- Benefits: Ideal for high-volume, repetitive production, minimizes reloading time, and enhances machine efficiency.
By incorporating these automation components, CNC machining can achieve high productivity, precision, and flexibility, enabling manufacturers to meet complex production demands while reducing costs and lead times.