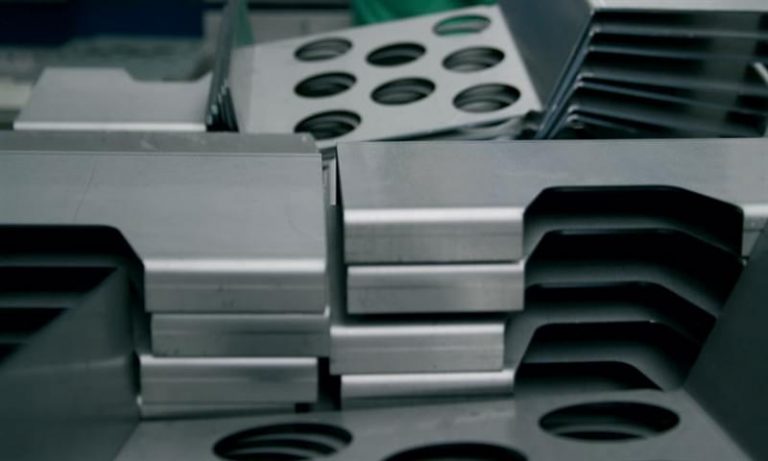
CNC Sheet Metal
CNC sheet metal fabrication is a process used to shape, cut, and form sheet metal into desired parts. It involves operations like cutting, bending, punching, and welding to achieve the final product. Here are the key steps involved in CNC sheet metal fabrication:
1. Design and Prepare the CAD Model
- Create a CAD Model: Design the part using CAD software, including all the necessary dimensions, cut patterns, bend lines, and holes.
- Generate CAM Files: Import the CAD model into CAM software to generate the tool paths and CNC code (G-code) for the machine. The CAM software will prepare the layout for cutting, bending, and forming operations.
2. Select the Material
- Choose the Sheet Metal: Based on the design and application, select the appropriate sheet metal type (e.g., aluminum, steel, stainless steel) and thickness.
- Cut to Size (if Necessary): If the sheet is too large for the CNC machine, pre-cut it to a manageable size.
3. Set Up the CNC Machine
- Prepare the Machine: Choose the appropriate CNC machine based on the operations required, such as a laser cutter, punch press, or press brake.
- Load Material: Place the sheet metal on the machine’s work area, securing it with clamps or vacuum fixtures to prevent movement during cutting or forming.
4. Load and Test the CNC Program
- Load the G-code: Transfer the G-code generated by the CAM software to the machine controller.
- Simulate or Dry Run (Optional): Run a simulation or dry run without material to ensure the tool paths, cut patterns, and bend positions are correct and there will be no collisions.
5. Execute Cutting Operations
- Start Cutting: Use the programmed CNC machine to perform the initial cutting operations. Common cutting processes include:
- Laser Cutting: Uses a focused laser to cut precise shapes in the sheet metal.
- Plasma Cutting: Uses a high-velocity plasma arc, suitable for thicker metals.
- Waterjet Cutting: Uses a high-pressure water jet, often mixed with abrasive particles, to cut materials without affecting metal properties.
- Punching: Creates holes, slots, or patterns by punching through the sheet metal with a punch press.
6. Forming and Bending Operations
- Set Up the Press Brake: If bending is required, set up a CNC press brake or bending machine with the correct tooling and angles.
- Program the Bending Sequence: Load the bending sequence from the CAM program or manually program the bends based on the required angles and part geometry.
- Perform the Bending: Sequentially bend the sheet metal along programmed lines to form the required shape, ensuring accuracy with each bend.
7. Additional Forming Operations (If Needed)
- Embossing, Beading, or Stamping: These processes add patterns or features to the metal, increasing its rigidity or for design purposes.
- Welding or Riveting: Join multiple pieces of sheet metal if the design requires assembling parts together.
8. Inspect the Part
- Check Dimensions and Bends: Use measurement tools to verify the part’s dimensions, angles, and hole positions meet the specifications.
- Inspect Surface Finish: Confirm there are no unwanted burrs, warping, or imperfections.
9. Post-Processing and Finishing
- Deburring: Remove sharp edges or burrs that may have formed during cutting or punching.
- Surface Finishing: Apply finishing processes like powder coating, painting, or polishing if specified in the design.
- Final Assembly: If the part is part of an assembly, perform any required joining or assembly steps here.
10. Clean Up and Document the Process
- Clean the Machine and Work Area: Remove any metal scraps, dust, or debris from the machine and the surrounding work area.
- Record Parameters: Document the machine settings, material information, and any adjustments made for future reference or repeat jobs.
This CNC sheet metal process allows for precise control over cutting and forming, producing complex parts with high accuracy. With CNC technology, designs can be quickly adjusted, allowing for flexible production and efficient repeatability.
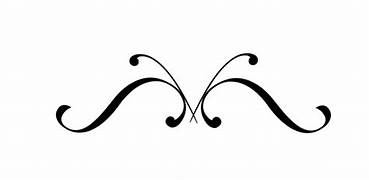