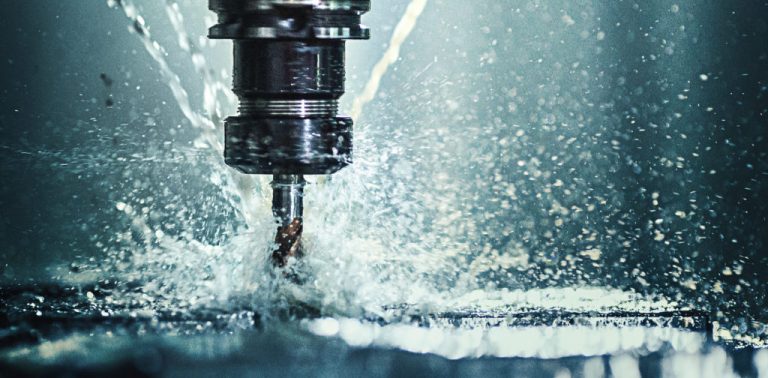
CNC Milling
CNC milling is a machining process where rotary cutters remove material from a workpiece by moving across multiple axes to create the desired shape. Here’s an overview of the typical CNC milling steps:
1. Prepare the Workpiece and Tools
- Select the Material: Choose the appropriate material (e.g., metal, plastic) and cut it to the necessary size if needed.
- Mount the Workpiece: Secure the workpiece onto the machine’s worktable using clamps, vises, or fixtures to prevent movement during machining.
- Choose Cutting Tools: Select the cutting tools (end mills, drills, etc.) based on the material, required cuts, and desired finish.
2. Set Up the CNC Machine
- Install Tools: Load the selected tools into the tool holder or spindle, ensuring they’re securely fastened.
- Calibrate Tool Offsets: Set tool offsets in the machine to define the position and length of each tool accurately, which helps prevent errors in tool positioning.
- Adjust Machine Parameters: Set spindle speed, feed rate, and depth of cut based on the material properties and tool specifications.
3. Create or Load the CNC Program
- Programming: Write the G-code program or use CAM software to generate tool paths from a CAD model. The code should specify tool movements, speeds, feeds, and the sequence of operations.
- Load the Program: Transfer the CNC code to the machine’s controller and verify it to ensure it matches the design intent.
- Review Toolpath: Simulate or visualize the program on the machine to confirm that it follows the correct paths and avoids collisions.
4. Run a Dry Run (Optional)
- Perform a “dry run” without the material (or at a very slow speed) to simulate tool movements along the programmed path.
- Confirm that the setup, work offsets, and program are correct before starting the actual machining process.
5. Begin the Machining Process
- Start the Spindle: Begin rotating the spindle to initiate cutting, adjusting the RPM and feed rate as specified in the program.
- Perform Milling Operations: The machine follows the program to execute a sequence of milling operations, which can include:
- Face Milling: Flattening the surface of the workpiece.
- Slot Milling: Creating grooves or channels.
- Contour Milling: Following the outline of a shape or profile.
- Drilling/Boring: Creating or enlarging holes.
- Pocket Milling: Removing material to create recesses or pockets.
6. Monitor and Adjust During Machining
- Keep an eye on tool wear, temperature, and surface finish throughout the process.
- Adjust coolant flow if necessary to reduce friction and keep the workpiece and tool cool.
- Make minor feed rate adjustments if required to maintain part quality.
7. Finish and Inspect the Part
- Remove the Workpiece: Carefully unmount the workpiece from the machine’s table.
- Inspect the Part: Use measuring tools like calipers, micrometers, or a CMM (Coordinate Measuring Machine) to ensure the dimensions and tolerances meet specifications.
- Post-Processing: Deburr, polish, or apply any additional surface finishing as needed.
8. Clean Up and Document the Process
- Clean the Machine: Remove swarf (metal shavings) and apply routine maintenance checks.
- Record Information: Document tool settings, cycle time, and machine parameters for future reference, especially for repeat jobs.
Each step in CNC milling requires precision and attention to detail to ensure the final part is produced accurately and efficiently. Proper tool selection, programming, and monitoring are key to a successful CNC milling process.
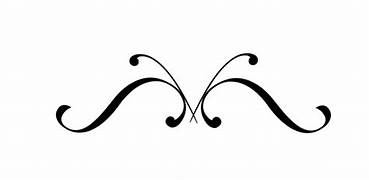