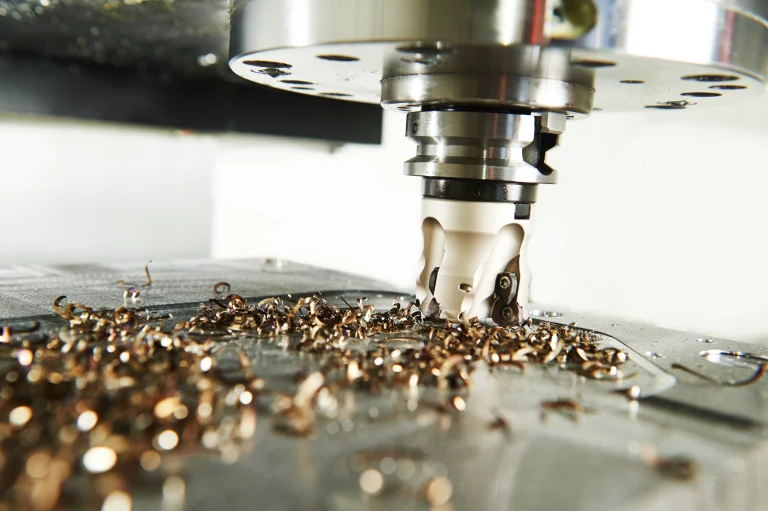
CNC Machining
CNC machining is an automated manufacturing process used to produce complex parts by removing material through various operations like drilling, milling, turning, and grinding. Here are the general steps involved in CNC machining:
1. Design the Part and Prepare the CAD Model
- Create a CAD Model: Design the part using CAD software, defining all the dimensions, shapes, and features.
- Convert to CAM Software: Import the CAD model into CAM (Computer-Aided Manufacturing) software to generate tool paths. The CAM software will create the CNC program (G-code) that the machine follows to produce the part.
2. Select the Material and Cutting Tools
- Choose the Material: Select a suitable raw material for the part based on design requirements (e.g., metal, plastic, or composite).
- Select Cutting Tools: Identify the appropriate cutting tools (e.g., end mills, drills, lathes) for the machining operations. The choice depends on the material properties and the operations required to shape the part.
3. Set Up the CNC Machine
- Mount the Workpiece: Secure the raw material on the machine’s table or in a chuck/fixture to ensure it remains stable throughout the machining process.
- Install Cutting Tools: Load the selected tools into the machine’s tool holder or turret.
- Calibrate Tool and Work Offsets: Set up the tool offsets (length and position of each tool) and define the work coordinate system, which tells the machine where the part is located relative to the machine’s zero point.
4. Load and Test the CNC Program
- Load G-Code: Upload the G-code generated by the CAM software into the CNC machine’s controller.
- Simulate the Program: Perform a simulation or “dry run” without the material to verify tool movements, check for potential errors, and ensure there will be no collisions or unexpected tool paths.
- Make Adjustments if Needed: Based on the dry run, modify any parameters in the program or machine settings for accuracy.
5. Execute the Machining Process
- Start the Spindle: Turn on the spindle to begin rotating the cutting tool at the programmed RPM.
- Begin Cutting Operations: The machine follows the G-code to execute the programmed operations, which could include:
- Facing: Flattening the top surface.
- Milling: Removing material to shape the part’s external features.
- Turning: Shaping the external or internal profile of cylindrical parts (if using a CNC lathe).
- Drilling/Boring: Creating or enlarging holes.
- Threading: Cutting threads into the material if needed.
- Coolant Flow: Ensure coolant is applied as needed to reduce heat buildup, minimize tool wear, and improve finish quality.
6. Monitor and Adjust During Machining
- Observe the cutting process to ensure tools remain sharp, temperatures stay manageable, and the part is shaping as expected.
- Adjust feed rates or speeds if necessary based on the machining conditions or to maintain desired quality.
7. Remove and Inspect the Finished Part
- Unmount the Workpiece: Carefully remove the finished part from the machine.
- Inspect Dimensions and Finish: Use measuring tools (calipers, micrometers, or CMMs) to verify that the part meets dimensional tolerances and surface finish specifications.
- Apply Post-Processing: Deburr, polish, or apply any additional finishing as needed to complete the part.
8. Clean Up and Document the Process
- Clean the Machine: Remove swarf (machining debris) and ensure the machine is clean for future use.
- Document Parameters: Record machining parameters, tool selections, and any other notes useful for repeat jobs or future adjustments.
Each step in CNC machining involves precise control and monitoring to produce high-quality, accurate parts. The use of CAD/CAM software, careful setup, and meticulous inspection are key to a successful CNC machining process.
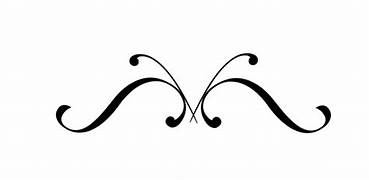